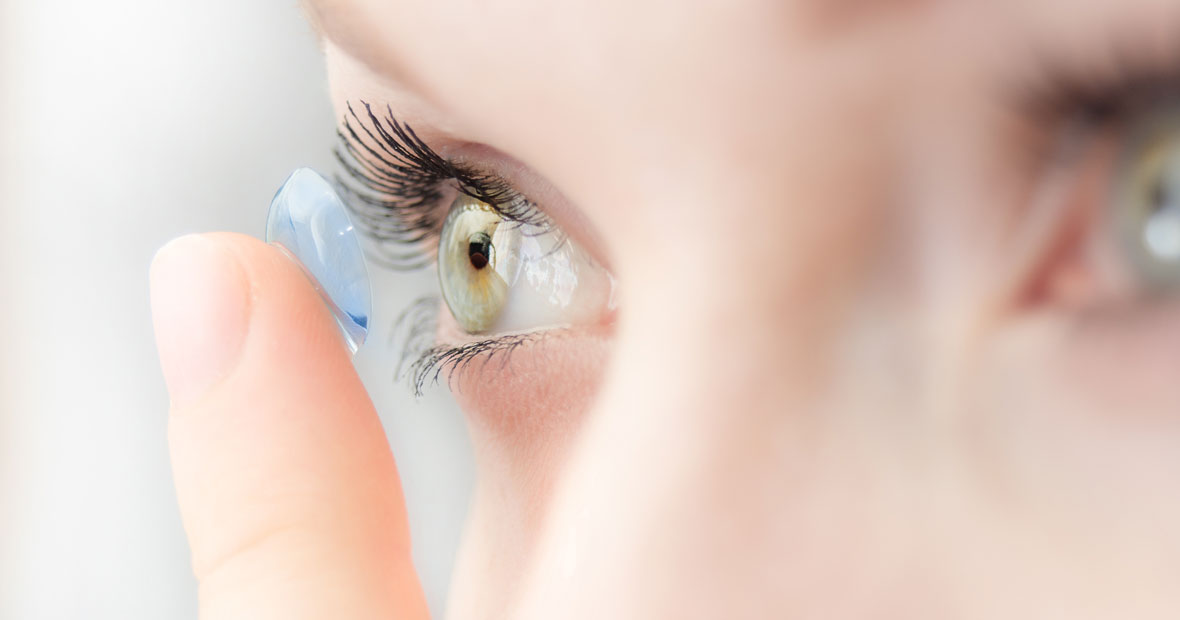
Vous faites partie des quatre millions de porteurs de lentilles de contact en France ? Ce dispositif optique a bien évolué depuis son invention il y a plus de deux siècles. Grâce aux innovations technologiques, la lentille devient plus souple et plus légère. Entre autres, elle n'assèche plus l'œil comme auparavant. Contrairement aux lunettes, elles sont discrètes. Comment tout ceci est-il possible ? Découvrez les étapes de fabrication d'une lentille de contact sur-mesure.
Origine des lentilles de contact
Les origines de ce dispositif optique remontent au XIXème siècle. Fabriquées en verre soufflé, les lentilles étaient lourdes et provoquaient de l'inconfort chez leur propriétaire. En raison de leur poids et de leur épaisseur, il fallait les enlever au bout de quelques heures. Malgré cela, leur invention prouvait qu'il était possible de corriger les troubles visuels autrement qu'avec des lunettes. Il ne restait plus qu'à trouver un matériau plus souple et léger pour remplacer le verre. Ce qui arriva dans les années 1960 grâce à la découverte de l'hydrogel. Tout en étant souple, le matériau est capable d'absorber l'eau. Néanmoins, les lentilles hydrogel puisent l'eau des yeux pour son hydratation. Ceci amène à une sècheresse oculaire. Grâce aux innovations technologiques, le silicone-hydrogel arrive quelques années plus tard. Considéré comme plus moderne, ce matériau procure à la fois de la souplesse et de la rigidité exigées chez une lentille de contact sur-mesure. Par ailleurs, les modèles en silicone-hydrogel sont perméables à l'oxygène et ne demandent pas une teneur élevée en eau. Différents types de lentilles existent sur le marché : rigide, souples, myopes, presbytes. Elles diffèrent également selon leur renouvèlement. Certaines lentilles sont changées quotidiennement, tandis que d'autres peuvent être portées pendant près d'un an. En somme, le matériau, la dimension, la fréquence de renouvèlement et le type de lentille sont des critères qui varient d'un individu à un autre. Ils peuvent même évoluer chez la même personne. D'où l'intérêt d'effectuer un suivi médical et de fabriquer une lentille de contact sur mesure.Les étapes de la fabrication de ce dispositif
Les lentilles de contact sont fabriquées dans des usines de fabrication partout dans le monde. La plupart d'entre elles se trouvent en Angleterre, en Hongrie et en Espagne. Certains experts proposant la fabrication sur mesure se trouvent en France. Dans les deux cas, la conception suit les étapes suivantes.La constitution des moules
Les moules représentent la première étape dans la fabrication de ce dispositif. La qualité de la finition des lentilles dépend de leur conception. Dans ce sens, il existe deux types de moules :- mâle : qui correspond à la courbure et la face postérieure de la lentille ;
- femelle : qui se trouve en dessous et est à l'origine de la puissance de la face antérieure.